東風標致307膜片彈簧離合器的設計
- 文件下載:
-
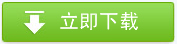
- 文件介紹:
- 該文件為 doc 格式,下載需要 1 積分
- 離合器是汽車傳動系統中直接與發動機相連接的部件。按動力傳遞順序來說,離合器應是傳動系中的第一總成。顧名思義,離合器是“離”與“合”矛盾的統一體。離合器的工作,就是受駕駛員操縱,或者分離,或者接合,以完成其本身的任務。離合器是設置在發動機與變速器之間的動力傳遞機構,其功用是能夠在必要時中斷動力的傳遞,保證汽車平穩地起步;保證傳動系換檔時工作平穩;限制傳動系所能承受的最大扭矩,防止傳動系過載。為使離合器起到以上幾個作用,目前汽車上廣泛采用彈簧壓緊的摩擦式離合器,摩擦離合器所能傳遞的最大扭矩取決于摩擦面間的工作壓緊力和摩擦片的尺寸以及摩擦面的表面狀況等,即主要取決于離合器基本參數和主要尺寸。膜片彈簧離合器在技術上比較先進,經濟性合理,同時其性能良好,使用可靠性高壽命長,結構簡單、緊湊,操作輕便。
1.2 離合器的功用
離合器可使發動機與傳動系逐漸接合,保證汽車平穩起步。現代車用活塞式發動機不能帶負荷啟動,它必須先在空負荷下啟動,然后再逐漸加載。發動機啟動后,得以穩定運轉的最低轉速約為300~500r/min,而汽車則只能由靜止開始起步,一個運轉著的發動機要帶一個靜止的傳動系,是不能突然剛性接合的。因為如果是突然的剛性連接,就必然造成不是汽車猛烈攢動,就是發動機熄火。所以離合器可使發動機與傳動系逐漸地柔和地接合在一起,使發動機加給傳動系的扭矩逐漸變大,至足以克服行駛阻力時,汽車便由靜止開始緩慢地平穩起步了。雖然利用變速器的空檔,也可以實現發動機與傳動系的分離。但變速器在空檔位置時,變速器內的主動齒輪和發動機還是連接的,要轉動發動機,就必須和變速器內的主動齒輪一起拖轉,而變速器內的齒輪浸在黏度較大的齒輪油中,拖轉它的阻力是很大的。尤其在寒冷季節,如果沒有離合器來分離發動機和傳動系,發動機起動是很困難的。所以離合器的第二個功能就是暫時分開發動機和傳動系的聯系,以便于發動機起動。汽車行駛中變速器要經常變換檔位,即變速器內的齒輪副要經常脫開嚙合和進入嚙合。如在脫檔時,由于原來嚙合的齒面壓力的存在,可能使脫檔困難,但如果用離合器暫時分離傳動系,即能便利脫檔.同時在掛檔時依靠駕駛員掌握,使待嚙合的齒輪副圓周速度達到同步是較為困難的,待嚙合齒輪副圓周速度的差異將會造成掛檔沖擊甚至掛不上檔,此時又需要離合器暫時分開傳動系,以便使與離合器主動齒輪聯結的質量減小,這樣即可以減小掛檔沖擊,以便于換檔。離合器所能傳遞的最大扭矩是有一定限制的,在汽車緊急制動時,傳動系受到很大的慣性負荷,此時由于離合器自動打滑,可避免傳動系零件超載損壞,起保護作用。
1.3 摩擦式離合器的基本機構原理
全套離合器應有兩部分組成:離合器和離合器操縱。
就摩擦式離合器本身而言,按其功能要求,結構上應由下列幾部分組成;主動件、從動件、壓緊彈簧和分離桿。其機構原理如圖1-3-1所示。
(A)接合
(B)分離
圖 1-3-1 膜片彈簧離合器分離接合示意圖
1-飛輪 2-從動盤總成 3-壓盤 4-分離桿 5-分離套筒 6-離合器制動 7-離合器踏板 8-壓緊彈簧 9-離合器蓋 10-變速器第一軸 11-分離拔叉及操縱連接桿
從圖1-3-1中可以看到,壓盤3、分離桿4和壓緊彈簧8一起組裝在離合器蓋9內,俗稱為離合器蓋總成。蓋總成通過螺栓安裝到發動機的飛輪上。飛輪1和壓蓋3為主動件,發動機的轉矩通過這兩個主動件輸入。飛輪1和壓盤3之間為從動盤總成2,它作為從動件通過摩擦接受由主動件傳來的輸入轉矩,并通過其中間的從動盤轂花鍵輸出轉矩(由變速器第一軸10接受)。壓緊彈簧8(它可以是螺旋彈簧或者膜片彈簧)通過壓盤3把從動盤總成緊緊壓在飛輪上,形成工作壓力。當發動機帶動飛輪1和壓盤3一道旋轉時,通過壓盤上壓緊彈簧產生的工作壓力所形成的摩擦力,帶動從動盤總成旋轉,完成轉矩的輸出。
如圖1-3-1(A)所示,離合器通常總是處于接合狀態。當需要切斷動力時,駕駛員通過離合器操縱系統中的踏板7,并經過操縱傳動桿系及分離拔叉11推動分離套筒5向前,消除間隙△Y,使分離桿4繞其在離合器蓋9上的支點轉動,克服壓緊彈簧8的工作壓力之后,壓盤3向后移動,從動盤總成2和壓盤3脫離接觸。離合器分離時的狀況如圖1-3-1(B)所示,此時,從動盤總成2不再輸出轉矩。分離套筒向左移動時,在消除間隙△r后,輸出軸10受到了制動,轉速很快下降。此種狀況稱為離合器的制動,其目的是為了容易換擋。但這種離合器制動主要用的重型離合器上,一般離合器不一定采用。分離桿和分離軸承之間的間隙△Y通常是需要的,因為從動盤總成因摩擦面磨損后會使壓盤3向左移動,如果這一移動受到分離軸承的限制,就會導致壓盤3不能很好地壓緊摩擦面,從而造成從動盤在傳扭時發生打滑現象。離合器使用一段時間后由于間隙△Y消失需要重新調整。現今許多離合器都設計有自動調整間隙的結構,此時間隙△Y就可以為零,并能在任何時候都保持零間隙而不影響離合器正常工作。這樣就省卻使用中需經常調整的麻煩。
1.4摩擦式離合器的分類和基本要求
摩擦式離合器結構類型較多,且可有多種組合。為了清除起見,用下列圖表顯示其相互關系。
圖1-4-1 汽車機械式離合器的結構分類圖
離合器的結構形式可以不相同,但在使用上對它的基本要求是一致的,他們應該是:
(1) 能可靠地傳遞發動機的最大轉矩;
(2) 接合過程要平順、柔和,使汽車起步時沒有抖動的沖擊;
(3) 分離時要迅速、徹底;
(4) 離合器從動部分的轉動慣量要小,以減輕換擋時變速器齒輪間的沖擊并方便換擋;
(5) 高速旋轉時具有可靠地強度,應注意平衡避免受離心力的影響;
(6) 操縱輕便,工作性能穩定,使用壽命長。
以上這些要求中最為重要的是使用可靠、壽命長以及和使用中的良好技術經濟和環保指標。
1.5 膜片彈簧離合器概述
膜片彈簧離合器是近年來在轎車和輕型載貨汽車上廣泛采用的一種離合器。因其作為壓簧,可以同時兼起分離杠桿的作用,使離合器的結構大為簡化,質量減小,并顯著地縮短了離合器的軸向尺寸。其次,由于膜片彈簧與壓盤以整個圓周接觸,使壓力分布均勻。另外由于膜片彈簧具有非線性彈性特性,故能在從動盤摩擦片磨損后,彈簧仍能可靠的傳遞發動機的轉矩,而不致產生滑離。離合器分離時,使離合器踏板操縱輕便,減輕駕駛員的勞動強度。此外,因膜片是一種對稱零件,平衡性好,在高速下,其壓緊力降低很少,而周布置彈簧離合器在高速時,因受離心力作用會產生橫向撓曲,彈簧嚴重鼓出,從而降低了對壓盤的壓緊力,從而引起離合器傳遞轉矩能力下。作為壓緊彈簧的所有膜片彈簧,是由彈簧鋼沖壓成的,具有“無底碟子”形狀的截錐形薄壁膜片,且自其小端在錐面上開有許多徑向切槽,以形成彈性杠桿,而且其余未切槽的大端截錐部分則起彈簧作用。膜片彈簧的兩側有支承圈,而后者借助于固定在離合器蓋上的一些(為徑向切槽數目的一半)鉚釘來安裝定位。當離合器蓋用螺栓固定到飛輪上時,由于離合器蓋靠向飛輪,后支承圈則壓膜片彈簧使其產生彈性變形,錐頂角變大,甚至膜片彈簧幾乎扁平。同時在膜片彈簧的大端對壓盤產生壓緊力使離合器處于結合狀態。當離合器分離時,分離軸承前移膜片彈簧壓前支承圈并以其作為支點發生反錐形的轉變,使膜片彈簧大端后移,并通過分離鉤拉動壓盤后移,使離合器分離。膜片彈簧離合器具有很多優點:首先,由于膜片彈簧具有非線性特性,因此設計摩擦片磨損后,彈簧壓力幾乎不變,且可以減輕分離離合器時的踏板力,使操縱輕便;其次,膜片彈簧的安裝位置對離合器軸的中心線是對稱的,因此其壓緊力實際上不受離心力的影響,性能穩定,平衡性也好;再者,膜片彈簧本身兼起壓緊彈簧和分離杠桿的作用,使離合器結構大為簡化,零件數目減小,質量減小并顯著縮短了軸向尺寸;另外,由于膜片彈簧與壓盤是以整個圓周接觸,使壓力分布均勻,摩擦片的接觸良好,摩擦均勻,也易于實現良好的通風散熱等。
由于膜片彈簧離合器具有上述一系列優點,并且制造膜片彈簧離合器的工藝水平在不斷提高,因此這種離合器在轎車及微型、輕型客車上得到廣泛運用,而且正大力擴展到載貨汽車和重型汽車上,國外已經設計出了傳遞轉矩為 、最大摩擦片外徑達420mm的膜片彈簧離合器系列,廣泛用于轎車、客車、輕型和中型貨車上。甚至某些總質量達 的重型汽車也有采用膜片彈簧離合器的,但膜片彈簧的制造成本比圓柱螺旋彈簧要高。膜片彈簧離合器的操縱內端的分離指處是承受壓力。當前膜片彈簧離合器的操縱機構已經為拉式操縱機構所取代。后者的膜片彈簧為反裝,并將支承圈移到膜片彈簧的大端附近,使結構簡化、零件減少、裝拆方便;膜片彈簧的應力分布也得到改善,最大應力下降;支承圈磨損后仍保持與膜片的接觸使離合器踏板的自由行程不受影響。而在壓式結構中支承圈的磨損會形成間隙而增大踏板的自由行程
2 離合器結構方案選取
2.1 由前面所提,本次所設計的離合器是針對東風標致307,所以通過網上數據的整理,我們可以知道東風標致307的基本數據(機型TU5JP4)
發動機最大功率及轉速 78kw/5750
發動機最大轉矩及轉速:142 /4000
汽車裝備質量:1293kg
主減速傳動比: =4.923
變速器1檔傳動比: =3.417
輪胎型號:195/65 R15 91V
汽車的驅動形式:4 2
最高車速:179km/h
滾動半徑:0.28m
整車質量:1293Kg
2.2 離合器設計的基本要求
為了保證離合器具有良好的工作性能,設計離合器應滿足以下要求:
1)在任何行駛條件下,都能可靠地傳遞發動機的最大轉矩,并有適當的轉矩儲備,又能防止傳動系過載。
2)接合時要完全、平順、柔和,保證汽車起步時沒有抖動和沖擊。
3 )分離要迅速、徹底。
4)從動部分轉動慣量要小,以減輕換檔時變速器齒輪間的沖擊,便于換檔和減小同步器的磨損。
5)具有足夠的吸熱能力和良好的通風散熱效果 ,以保證工作溫度不致過高,延長其使用壽命。
6)應能避免和衰減傳動系的扭轉振動,并具有吸收振動、緩和沖擊和降低噪聲的能力。
7)操縱輕便、準確,以減輕駕駛員的疲勞。
8)作用在從動盤上的總壓力和摩擦離合器和摩擦材料的摩擦因數在離合器工作過程中變化盡可能小,以保證有穩定的工作性能。
9)具有足夠的強度和良 好的動平衡,以保證其工作可靠、使用壽命長。
10)結構應簡單、緊湊,質量小,制造工藝性好,拆裝、維修、調整方便等
2.3 離合器結構設計
2.3.1 摩擦片的選擇
單片因為結構簡單,尺寸緊湊,散熱良好,維修調整方便,從動部分轉動慣量小,在使用時能保證分離徹底接合平順,所以被廣泛使用與轎車和中、小型貨車.因此本設計選擇單片離合器。
2.3.2 壓緊彈簧布置形式的選擇
離合器壓緊裝置可分為周布彈簧式、中央彈簧式、斜置彈簧式、膜片彈簧式等。其中膜片彈簧的主要特點是用一個膜片彈簧代替螺旋彈簧和分離杠桿。膜片彈簧與其他幾類相比又有以下幾個優點:
1)由于膜片彈簧有理想的非線性特征,彈簧壓力在摩擦片磨損范圍內能保證大致不變。當離合器分離時,彈簧壓力不像圓柱彈簧那樣升高,而是降低,從而降低踏板力;
2)膜片彈簧兼 起壓緊彈簧和分離杠桿的作用,使結構簡單緊湊,軸向尺寸小,零件數目少,質量小 ;
3)高速旋轉時,壓緊力降低很少,性能較穩定;而圓柱彈簧壓緊力明顯下降;4 )由于膜片彈簧大端面環形與壓盤接觸,故其壓力分布均勻,摩擦片磨損均勻,可提高使用壽命;
5)易于實現良好的通風散熱,使用壽命長;
6)平衡性好;
7)有利于大批量生產,降低制造成本。但膜片彈簧的制造工藝較復雜,對材料質量和尺寸精度要求高,其非線性特性在生產中不易控制,開口處容易產生裂紋,端部容易磨損 。
近年來,由于材料性能的提高,制造工藝和設計方法的逐步完善,膜片彈簧的制造已日趨成熟。因此,我選用膜片彈簧式離合器,材料選取為60Si2MnA。
2.3.3 壓盤的驅動方式
壓盤的驅動形式主要有凸塊式、窗孔式、傳力銷式、鍵塊式和彈性傳動片式等多種。前三種的共同缺點是在連接件之間都有間隙,在傳動中將產生沖擊和噪聲,而且在零件相對滑動中有摩擦和磨損,降低了離合器的傳動效率 。彈性傳動片式是近年來廣泛采用的驅動形式,沿圓周切向布置得三組或四組薄彈簧傳動片兩端分別與離合器蓋和壓盤以鉚釘或螺釘聯結,傳動片的彈性允許其軸向移動。當發動機驅動時,傳動片受拉,當拖動發動機時,傳動片受壓。彈性傳動片驅動方式的結構簡單,壓盤與飛輪對中性能好,使用平衡性好,工作可靠,壽命長。壓盤形狀較復雜,要求傳熱性好,具有較高的摩擦因數,通常采用灰鑄鐵,一般采用 HT200 、HT250、HT300,硬度為170~227HBS。也有少數采用合金壓鑄件。故而,壓盤的驅動方式選擇彈性傳動片式,材料選用HT200。
2.3.4 離合器的散熱通風
試驗表明,摩擦片的磨損是隨壓盤溫度的升高而增大的,當壓盤工作表面超過180~200C時摩擦片磨損劇烈增加,正常使用條件的離合器壓盤工作表面的瞬時溫度一般在180C以下。在特別頻繁的使用下,壓盤表面的瞬時溫度有可能達到1000C。過高的溫度能使壓盤受壓變形產生裂紋和碎裂 。為使摩擦表面溫度不致過高,除要求壓盤有足夠大的質量以保證足夠的熱容量外,還要散熱通風好。改善離合器散熱通風結構的措施有:在壓盤上設置散熱筋,或鼓風筋;在離合器中間壓盤內鑄通風槽;將離合器蓋和壓桿制成特殊的葉輪形狀,用以鼓風;在離合器外殼內裝導流罩。膜片彈簧式離合器本身構造能良好實現通風散熱效果,故不需作另外設置。
2.4 摩擦片厚度報警器
離合器是靠摩擦力來傳遞動力的。離合器的摩擦片也由于摩擦而不斷磨損,當摩擦片磨損到一定程度后,就需要對其進行處理或更換摩擦片。但是摩擦片是安裝在離合器內的,很難及時處理或更換已磨損了的摩擦片。所以需要一個報警器來及時提醒駕駛員更換已磨損到了一定程度的摩擦片。鑒于以上情況,應該在離合器內安裝摩擦片厚度報警器。摩擦片厚度報警器的工作原理很簡單,當摩擦片被磨薄到一定程度的時候,壓盤會向飛輪方向移動,在壓盤上安裝的傳動片會隨著壓盤向飛輪方向移動,進而與報警器上的鉤子擠壓,鉤子與感應觸手接合在一起,當鉤子被擠壓時,感應觸手會因拉緊彈簧的原因被拉起,與傳感器接觸,進而實施報警,使駕駛員及時更換摩擦片。
3.離合器基本結構參數的確定
3.1 摩擦片主要參數的選擇
摩擦片外徑是離合器的主要參數,它對離合器的輪廓尺寸、質量和使用壽命有決定性的影響。當離合器結構形式及摩擦片材料已選定,發動機最大轉矩已知,適當選取后備系數β和單位壓力Ρ,可估算出摩擦片外徑。摩擦片外徑Dmm也可以根據發動機最大轉矩Temax( )按如下經驗公式來計算 式中:系數A反映了不同結構和使用條件對D的影響,本次設計主要針對的是對小轎車的設計故本次A選擇 47 。按Teamx初選D以后,還需注意摩擦片尺寸的系列化和標準化,圖3-1-1為我國摩擦片尺寸的標準。
表 3-1-1 離合器摩擦片尺寸系列和參數
外徑D/mm 160 180 200 225 250 280 300 325 350 380 405 430
內徑d/mm 110 125 140 150 155 165 175 190 195 205 220 230
厚度/mm 3.2 3.5 3.5 3.5 3.5 3.5 3.5 3.5 4 4 4 4
C’=d/D 0.687 0.694 0.070 0.667 0.620 0.589 0.583 0.585 0.557 0.540 0.543 0.535
1-C’3 0.676 0.667 0.657 0.703 0.762 0.796 0..802 0.800 0.827 0.843 0.840 0.847
單面面積/CM2 106 132 160 221 302 402 466 546 678 729 908 1037
摩擦片內徑d不作為一個獨立的參數,它和外徑D有一定關系,用比值C’來反映,定義為 C’=d/D 比值C’關系到從動片總成的結構設計和使用性能。具體來說,由于現在廣泛采用扭轉減震器,所以布置扭轉減震器時要求加大內徑d ,從而C’要變大;但過分加大C’值會使摩擦面積變小,這也是不利的。按照目前的設計經驗,推薦 C’= 對摩擦片厚度h ,我國已規定了3種規格:3.2 , 3.5 , 4 ,無更多選擇余地。
根據以上數據所以選擇外徑D = 180 d=125 厚度h=3.5 單位面積 a=132
內徑與外徑比 C’=0.694 1-C’3=0.667
3.2 離合器后備系數β的確定
后備系數β是離合器的重要參數,反映離合器傳遞發動機最大扭矩的可靠程度,選擇β時,應從以下幾個反面考慮:
A.摩擦片在使用中有一定磨損后,離合器還能確保傳遞發動機最大扭矩;
B.防止離合器本身滑磨程度過大;
C.要求能夠防止傳動系過載。通常轎車和輕型貨車β= 本設計的是輕型轎車,故可以選取β=1.2.
3.3 單位壓力P的確定
摩擦面上的單位壓力Ρ的值和離合器本身的工作條件,摩擦片的直徑大小,后備系數,摩擦片材料及質量等有關。離合器使用頻繁,工作條件比較惡劣(如城市用的公共汽車和礦用載重車),單位壓力Ρ較小為好。當摩擦片的外徑較大時也要適當降低摩擦片摩擦面上的單位壓力Ρ。因為在其它條件不變的情況下,由于摩擦片外徑的增加,摩擦片外緣線速度大,滑磨時發熱厲害,再加上因整個零件較大,零件的溫度梯度也大,零件受熱不均勻,為了避免這些不利因素,單位壓力Ρ應隨摩擦片外徑的增加而降低。
對于采用有機材料作為基礎的摩擦片,下列一些數據可以作為參考。
對于小轎車,D≤230 時,p約為0.25 ;D≥230 時,p可由下列選取:
對于載貨車,D=230 時,p約為0.2 ;D= 時,p約為0.14
對于城市公共汽車,一般單片離合器P約為0.13 ;大的雙片離合器p約為0.1
現在一些重型車輛采用耐熱性能更好的陶瓷材料作為摩擦副元件,它的單位壓力允許更高。國外推薦值為 目前我國研制使用的陶瓷片,其設計值約等于0.4 針對本次設計的汽車離合器,我們知道D=180 <230 所以我們可以選取P=0.25
4. 離合器從動盤設計
4.1 從動盤結構介紹
在現代汽車上,一般都采用帶有扭轉減振的從動盤,用以避免汽車傳動系統的共振,緩和沖擊,減少噪聲,提高傳動系統零件的壽命,改善汽車行駛的舒適性,并使汽車平穩起步。從動盤主要由從動片,從動盤轂,摩擦片等組成,由下圖
圖 4-1 帶有扭轉減振器的從動盤
4.2 從動盤設計應滿足的要求
從動盤總成由摩擦片、從動片、扭轉減振器和從動盤轂等組成。它雖然對離合器工作性能影響很大的構件,但是其工作壽命薄弱,因此在結構和材料上的選擇是設計的重點。從動盤總成應滿足如下設計要求:
1)為了減少變速器換擋時齒輪間沖擊 ,從動盤的轉動慣量應盡可能小。
2)為了保證汽車平穩起步、摩擦面片上的壓力分布均勻等從動盤應具有軸向彈性。
3)為了避免傳動系的扭轉共振以及緩和沖擊載荷 ,從動盤中應裝有扭轉減振器。
4)要有足夠的抗爆裂強度。
...